El mantenimiento predictivo o “Predictive Maintenance” — PdM, a menudo puede ser observado como la panacea de los problemas de mantenimientos actuales.
Sin embargo, iniciar un programa de este tipo puede ser complejo, costoso y es posible que no todas las instalaciones estén preparadas para dicho programa.
No se trata de una tarea fácil, por lo que hemos elaborado esta guía completa para ayudarte a dividir el proceso tomando en cuenta las mejores prácticas para optimizar su instalación.
Todos piensan en el mantenimiento predictivo como una forma de anticipar posibles averías y fallas en las maquinarias y, esencialmente, “detectarlos justo a tiempo”. Aunque esto es una gran parte, no es el núcleo.
En efecto, es mucho más. Se centra en utilizar las condiciones operativas reales de sus activos para optimizar la implementación en su conjunto.
Debemos iniciar por establecer una mentalidad y una cultura de mantenimiento predictivo, seguido de un liderazgo fuerte, visionario y experto, así como un equipo capacitado y motivado.
Una vez que tengamos a las personas adecuadas en su lugar, tendremos que verificar los procesos y tecnologías que están utilizando actualmente.
Si estás operando en un modo principalmente reactivo, lo primero que deberás hacer es iniciar la transición a uno preventivo, para lo que necesitarás las herramientas adecuadas para manejar nuevos procesos para tus activos complejos.
Implementa o perfecciona el Internet Industrial de las Cosas —IIoT- o un sistema de mantenimiento computarizado para que sirva como base de la actualización de mantenimiento y contribuya en el respaldo de tecnología de mantenimiento predictivo.
¿Quieres aprender más sobre el tema? En las siguientes líneas encontrarás los 9 consejos más efectivos para el mantenimiento preventivo en las industrias.
¡No te lo pierdas, quédate con nosotros!
1. Comienza con algo pequeño
En definitiva, ninguna empresa tiene recursos ilimitados. Incluso con la actitud correcta, nos enfrentaremos a cierto nivel de escepticismo y cantidad de inversión cada vez que implementemos un nuevo sistema; por lo que es importante empezar de a poco.
Selecciona uno o dos activos críticos para probar a través de una aplicación de mantenimiento predictivo inicial. De esta manera, podremos tomar medidas con lentitud y abordar los errores sin afectar una gran cantidad de activos.
No hay nada como un plan piloto exitoso para generar el impulso que requerimos para expandir un programa efectivo.
2. Identifica activos listos para PdM
Determina qué activos están preparados o merecen un lugar en tu nuevo programa de mantenimiento predictivo.
¡Ojo! Para alguno de ellos, simplemente el PdM no es el enfoque correcto; pueden ser prescindibles o requerir soluciones de bajo costo. Además, no querrás poner a prueba un nuevo programa en tu activo más caro o importante.
A modo de precaución, hay que comenzar el programa de mantenimiento predictivo con una pieza de equipo menos significativa para que, a medida que escalamos a otros más críticos, los procesos sean mejores de lo que eran originalmente.
Para decidir qué activos son los más críticos, comienza con los códigos de falla debido a que se basan en bienes o en inspecciones.
Existen varias maneras para lograrlo, incluyendo:
Códigos de fallas
En este sentido, los códigos de falla comunes significan malas prácticas de mantenimiento, errores del usuario o del operador, problemas de calibración y defecto de los equipos.
Es posible que algunos códigos de falla no afecten el rendimiento inmediato, pero otros pueden causar un tiempo de inactividad significativo.
Tipo y cantidad de tareas
Otra forma de categorizar los bienes es por el tipo y la cantidad de tareas necesarias para mantenerlos.
Por ejemplo, las tareas de valor agregado, de calibración integrales, tareas especializadas, de intervalo y repetibles, deben tenerse en cuenta porque todas exigen un gran número de recursos humanos y financieros.
Evalúa tanto los códigos de falla como las tareas de mantenimiento, así como el historial y el estado de bienes particulares. Las averías frecuentes indican altos costos de reparación y mucho tiempo de inactividad.
Piensa en lo importante que es un activo para tu línea de producción diaria. Si una máquina se usa con poca frecuencia, probablemente pueda esperar.
El candidato ideal para un activo piloto es uno que se usa moderadamente y que a menudo se descompone, significando un problema potencial para la organización.
Es por esta razón que es importante abordarlo y no sufriremos grandes pérdidas si el programa de mantenimiento predictivo tarda un poco en perfeccionarse.
3. Identifica los recursos necesarios
Lo siguiente que debes hacer es analizar todos los recursos que necesitarás para la implementación del programa de mantenimiento predictivo en tu empresa.
A continuación, te explicamos en detalle las categorías clave:
Cantidad de tiempo de las labores
Analiza la cantidad de horas que requerirás para iniciar y ejecutar el programa. Esto debe incluir las horas de supervisión, administración, planificación, actualización, horas totales de artesanía por sector laboral y nivel de habilidad.
También vas a necesitar horas de personal de apoyo; estos deben incluir no solo la asistencia administrativa, sino también los departamentos y el manejo de materiales.
Materiales necesarios
Dependiendo del activo crítico con el que decidas comenzar, deberás identificar los materiales necesarios para seguir adelante.
Lo que normalmente incluye: qué artículos, cantidad que necesitamos almacenar y cuándo reponer.
Instalaciones a utilizar
Resulta indispensable verificar detenidamente el espacio físico y definir dónde se llevarán a cabo las tareas preventivas.
Por lo que deberás tener en cuenta: dónde establecer el taller, cuarto de herramientas, inventario, capacitación y espacio para reparaciones.
Tecnología aplicable
En el contexto digital en el que se desenvuelven las industrias en la actualidad, es fundamental buscar minuciosamente entre la disponibilidad de herramientas y herramientas digitales que optimicen la gestión.
Expresa con precisión qué recolectores de datos en Big Data o tecnologías del Internet Industrial de las Cosas —IIoT- podrás aprovechar, como los tipos de sensores, cámaras infrarrojas y softwares de análisis. ¡Sobre esto hablaremos luego!
Capacitación del personal
Invertir en tu equipo en términos de capacitación industrial es una tarea que no puede faltar y, si quieres agregarle un poco más de profesionalismo, podrías adoptar en tu empresa la academia 4.0.
Se trata de una plataforma totalmente en línea que es utilizada para capacitar al personal de una empresa sobre las nuevas tendencias en la industria como, por ejemplo, 3D Experience, ingeniería digital, SOLIDWORKS, entre muchos otros.
Podrán, incluso, optar por una certificación que es otorgada al finalizar. En otras palabras, tendrás una mano de obra más especializada para la planificación, desarrollo y ejecución del programa de mantenimiento predictivo.
4. Implementar la supervisión de activos y comenzar la recopilación de datos
En este punto, ya podremos iniciar a monitorear el activo piloto, por lo que debemos supervisarlo durante todo el tiempo que podamos antes de implementar el programa de PdM.
Estos datos de referencia se vuelven cruciales, ya que son la base de todo nuestro programa piloto.
A medida que vayan surgiendo señales de alerta o fallas, hay que realizar y registrar el mantenimiento necesario.
Por otro lado, hay que examinar los registros de la máquina y recopilar información del fabricante sobre tareas de mantenimiento, frecuencia, seguridad, etcétera, e incluye conversaciones con técnicos u operadores de especializados con nuestro activo piloto.
El personal de consulta sobre el conocimiento práctico del equipo nos dará información única que es posible que no podamos extraer de datos duros.
Invierte en los sensores que sean necesarios en todo el equipo y comienza a recopilar datos para el mantenimiento predictivo.
Estos aparatos monitorearán las condiciones actuales, así como los códigos de falla del equipo, la cual, será muy específica para el activo crítico que seleccionemos.
Tres de las vías más comunes para la recopilación de datos en las instalaciones son:
Sistemas electromecánicos
Los sensores de vibración y el monitoreo generalmente juegan un papel principal en el mantenimiento predictivo.
En muchos casos, los recolectores de datos y el software deben trabajar juntos para captar, dar seguimiento y evaluar la energía de vibración.
Termografía
Se encarga de monitorear la energía infrarroja como una manera de verificar las condiciones de la maquinaria.
SI ciertas áreas de la superficie generan demasiado o no suficiente calor, un PdM puede notificar a un técnico que explore el problema.
Lubricación y desgaste
Checar las condiciones del aceite de los equipos y desgaste con regularidad nos ayudará a tomar decisiones sobre la frecuencia de los cambios de aceite en el equipo.
Tradicionalmente, esto ha sido determinado con el uso.
No obstante, con la tecnología de mantenimiento predictivo, podremos utilizar datos reales de lubricación y desgaste para garantizar que el mantenimiento se complete en el momento adecuado.
5. Desarrolla algoritmos de Machine Learning para predecir fallas
Todo lo que hemos mencionado hasta ahora, comienza a juntarse con este consejo.
Al utilizar datos que estamos recopilando con los sensores, podremos desarrollar algoritmos que predecirán la falla del equipo antes de que realmente ocurra.
Muchas instalaciones utilizan el Análisis Modal de Fallos y Efectos —FMEA. Esto es una herramienta de análisis de procesos sistemáticos que contribuye a captar los modos de falla, efectos y causas; también analiza la frecuencia, la tasa de detección y gravedad.
Las fórmulas, los algoritmos y los procesos de Machine Learning —aprendizaje automático de máquinas, pueden utilizar estos datos para la evaluación de las condiciones actuales de los activos críticos, así como para predecir el tiempo restante antes de que ocurra una nueva falla.
Estos son algoritmos de pronóstico, que comparan el estado de la máquina en el momento con los datos de referencia que trabajó arduamente para recabar y estimar cuándo se estima que suceda el problema potencial.
Dependiendo de la industria e instalación, podrás utilizar una amplia gama de algoritmo; deberás acumular suficiente información valiosa utilizándolos para tomar decisiones de mantenimiento inteligentes y mejorar aún más el programa de mantenimiento predictivo.
6. Implementa el activo piloto
Ahora que tenemos el monitoreo en su lugar —una recopilación continua de datos, y los algoritmos para procesarlos, nuestra tecnología está lista para funcionar; ahora hay que aplicarlo al activo piloto.
“Aplicar” el análisis predictivo en el equipo de prueba puede ser de este modo:
- Los sensores recopilan datos y los envían a la nube.
- Los algoritmos PdM se aplican al centro de datos.
- Se generan informes y conocimientos en tiempo real.
Los datos y análisis basados en la nube automatizan la recopilación, el almacenamiento y la evaluación de información, lo que hace que todo el proceso sea increíblemente rápido.
En esta misma línea, podemos disponer de un claro ejemplo:
Si los sensores de vibración que instalamos en la maquinaria detectan un exceso de ruido o movimiento de vibración, van a ser identificado como una anomalía al comparar estos datos con otros de referencia o con las especificaciones de la máquina.
Esta tecnología predictiva determina la ubicación y la causa del potencial problema incluso antes de que ocurra.
Una vez que se resuelve el inconveniente, los sensores volverán a monitorear continuamente la solución para asegurarse de que sea efectiva.
7. Establece un proceso continuo de implementación y mejora
Una vez que hayas tenido éxito en tu estrategia de mantenimiento predictivo, querrás poner en marcha un ciclo de implementación y mejora a medida que incorporas los demás equipos que faltan.
Asegúrate de ejecutar de ejecutar los datos para compararlos con las Métricas —KPI- preestablecidas para que puedas ilustrar el Retorno de la Inversión —ROI- y justificar una oportuna expansión.
Según los expertos de la industria, dos de las razones clave por las que falla la aplicación del mantenimiento predictivo en una empresa es la falta de coherencia y metodología a largo plazo.
Para que un programa funcione, se desarrolle y evolucione, las instalaciones deben monitorear los datos de los activos críticos regular y continuamente. Esto significa que los procesos deben entenderse y establecerse correctamente.
A medida que vamos experimentando la rotación de técnicos y talentos, debemos poder transferir el conocimiento entre lo tradicional y lo innovador, para mantener el programa actualizado, en movimiento y adaptado a las nuevas tendencias de la industria.
El estudio también afirma que podemos esperar un ahorro de costos entre un 5% al 10% en operaciones, mantenimiento y gastos de reparación. Los costos generales de mantenimiento también verán una disminución.
8. Haz que los empleados sean responsables del mantenimiento
Ya habiendo identificado qué actividades de mantenimiento predictivo deben realizarse y cuándo, ahora toca asignar la responsabilidad de seguimiento a un coordinador de mantenimiento, operador de la máquina u otro personal apropiado.
Debes hacer que estos empleados designados firmen las actividades de mantenimiento en una hoja adjunta a cada máquina, a través de un software o mediante informes diarios, semanales y mensuales enviadas a los supervisores.
Independientemente del método que elijamos para el seguimiento, hay que monitorear constantemente el programa de mantenimiento predictivo que hemos diseñado.
9. Aplica soluciones del Internet de las Cosas Industrial
A través de una combinación de datos en tiempo real recopilados mediante el Internet de las Cosas Industrial (IIoT), el mantenimiento predictivo analiza continuamente el estado del equipo durante las operaciones para reducir la posibilidad de fallas inesperadas de la máquina.
Con el PdM, las organizaciones pueden llevar un seguimiento y probar varios indicadores, como una velocidad de giro lenta, lubricación o temperatura.
Usando un monitoreo basado en las condiciones y el IIoT, estas herramientas detectan inconvenientes durante las operaciones normales y envían señales de alerta en tiempo real al propietario de la máquina que indican un potencial problema futuro.
¿Cuál es el rol del IIoT en el mantenimiento predictivo?
En definitiva, la llegada del Internet de las Cosas en las industrias está cambiando la forma en la que hacemos el mantenimiento predictivo.
Ahora podemos tener dispositivos de monitoreo actualizados en todo momento, detectar si algo va mal con la máquina o utilizar el Machine Learning para hacer predicciones.
Este es el nuevo enfoque del PdM, a lo que se le denomina: Mantenimiento predictivo basado en el IIoT.
Estos son los cuatro bloques principales de cómo han evolucionado las tareas de mantenimiento:
- Mantenimiento reactivo.
- Mantenimiento preventivo.
- Mantenimiento predictivo manual.
- Mantenimiento predictivo basado en el IIoT —donde estamos ahora.
Actualmente, podemos aprovechar la instalación de herramientas en cualquiera de nuestras maquinarias para medir su capacidad productiva e incluso, analizar si existe algún problema potencial en ella.
Combina datos contextuales y en tiempo real
Hasta ahora, estamos obteniendo información sobre el estado del equipo y luego, basándonos en eso, podemos planificar las intervenciones.
Tenemos la oportunidad de tomar un sensor o una combinación de muchos de ellos y fuentes de datos.
Los desafíos tradicionales del mantenimiento predictivo era la limitación de datos en un mismo sensor. Por lo que se utilizaba principalmente para el control operativo, donde se necesitaba controlar las máquinas, hacerlas más rápidas, lentas, encenderlas o apagarlas.
Aprendizaje automático a escala
El mantenimiento predictivo a menudo se basaba en análisis predictivos que requerían científicos de datos expertos y modelos complejos de aprendizaje automático.
Esto significaba que el aprendizaje automático se limitaba a grandes organizaciones que tenían suficiente capacidad financiera para llevar esta inversión.
Sin embargo, incluso en esas grandes empresas, debían hacerlo por lotes. Los operarios tenían que salir y tomar manualmente la lectura de datos y colocarlos en las herramientas de aprendizaje automático para elaborar cronogramas.
Mucho ha cambiado desde entonces. Ahora tenemos la capacidad de analizar datos continuamente a través de modelos basados en el Machine Learning y obtener predicciones en simultáneo.
Y, al haber mayor demanda en este tipo de tecnologías, los costos de adquisición han bajado y su calidad no ha parado de incrementar, por lo que ya no está reservado solo para grandes organizaciones.
4 ventajas de un buen mantenimiento predictivo
¡Hasta acá ya conoces las mejores prácticas a tener en cuenta para lograr un mantenimiento predictivo efectivo!
No obstante, ¿cuáles son las principales ventajas de contar con uno? A continuación, encontrarás las 4 más relevantes:
Menos fallas en el equipo
Gracias a la adopción de las tecnologías del Internet Industrial de las Cosas, con el monitoreo de las condiciones del equipo en tiempo real y los sistemas de proceso de manera regular, se puede reducir el número de fallas repentinas de la máquina en más del 50%.
Mayor vida útil de los activos
Aprovechar el aprendizaje automático para detectar problemas potenciales en los equipos y sistemas de manera temprana, aumenta la vida útil de la máquina en un promedio del 30%.
Después de implementar una estrategia de mantenimiento predictivo, las organizaciones reducen no solo la gravedad de daños, sino que también disminuyen la propagación de defectos.
Datos precisos de los equipos
Una de las ventajas del mantenimiento predictivo es la capacidad del software de usar datos de sensores para hacer predicciones sobre el tiempo medio entre fallas —MTBF.
Tener acceso a esta información valiosa permite a los administradores de las instalaciones determinar el momento más rentable para reemplazar la maquinaria, en lugar de seguir programando costosas tareas de mantenimiento que no mantendrán el equipo en óptimas condiciones.
A través de los algoritmos, podremos detallar cuándo los costos de mantenimiento y operación continua superan los costos de reemplazo.
Con esto, es mucho más sencillo tomar una decisión segura.
Verificación de la eficacia de las reparaciones
Como mencionamos algunos párrafos atrás, los sensores de mantenimiento predictivo se pueden utilizar para realizar análisis de vibraciones, lubricación (medición del nivel de aceite), imágenes térmicas, observación de equipos, y más.
Los sensores de PdM también son empleados para comprobar si una reparación se ha efectuado correctamente antes de que la máquina vuelva a arrancar.
Esto aumenta la seguridad y elimina la necesidad de un segundo apagado, que suele ser necesario para ajustar reparaciones inadecuadas o incompletas.
¡Muy bien! Llegado hasta este punto tienes mucha información valiosa para implementar en tu empresa.
Ahora bien, ¿quieres aprender más sobre la aplicación del IoT en las industrias? De ser así, tan solo debes conectar con nuestro artículo dedicado al tema:
Conectividad industrial: ¿Por qué es clave en estos tiempos?
Etiquetas:
Artículos relacionados
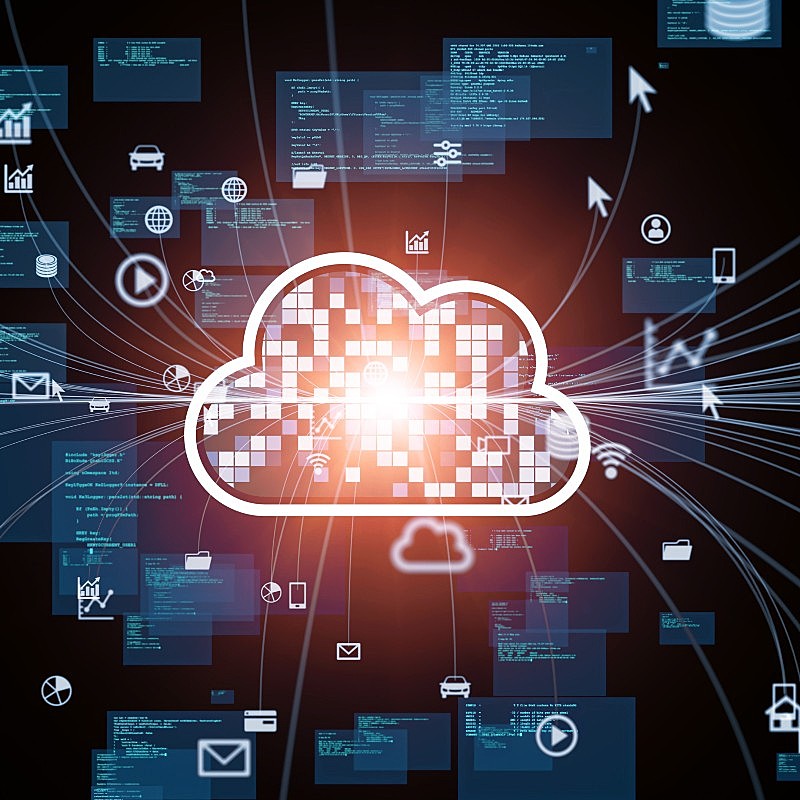
Introducción a la Latencia en la Comunicación y el IoT La latencia es un factor determinante en la comunicación entre dispositivos, especialmente en el Internet de las Cosas en la Industria (IoT). Si alguna vez has experimentado tiempos de espera prolongados al cargar una página web o realizar una videollamada, ya has sentido los efectos de […]
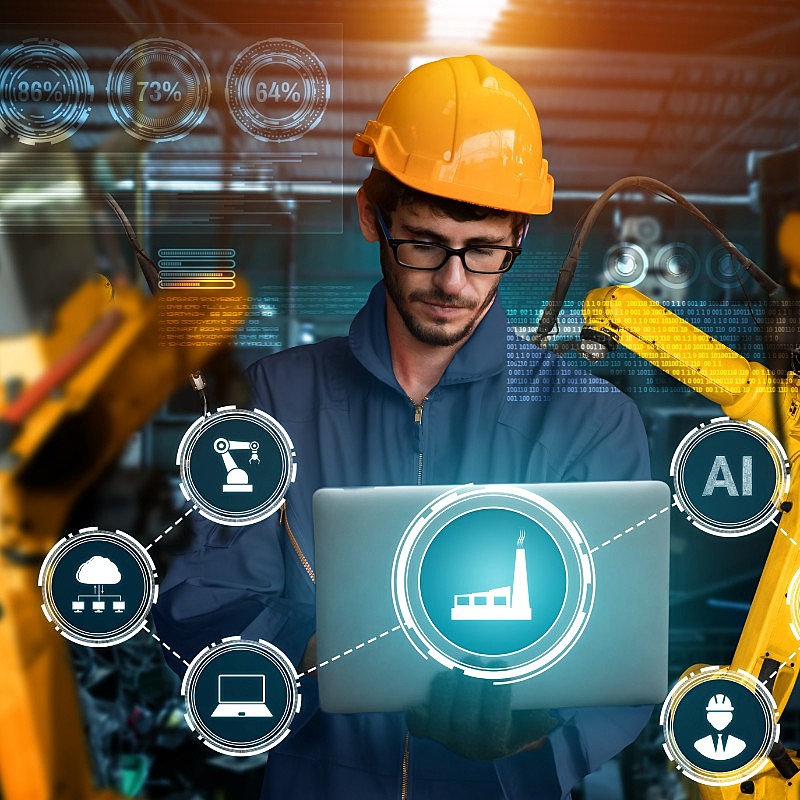
El Poder del IIoT en la Industria Manufacturera En la era de la Industria 4.0, la eficiencia operativa se ha convertido en una necesidad crítica para mantenerse competitivo en el mercado global. El Internet de las Cosas Industrial (IIoT) está transformando fábricas al permitir la conectividad entre equipos, recopilando datos en tiempo real y optimizando procesos. Implementar IIoT […]
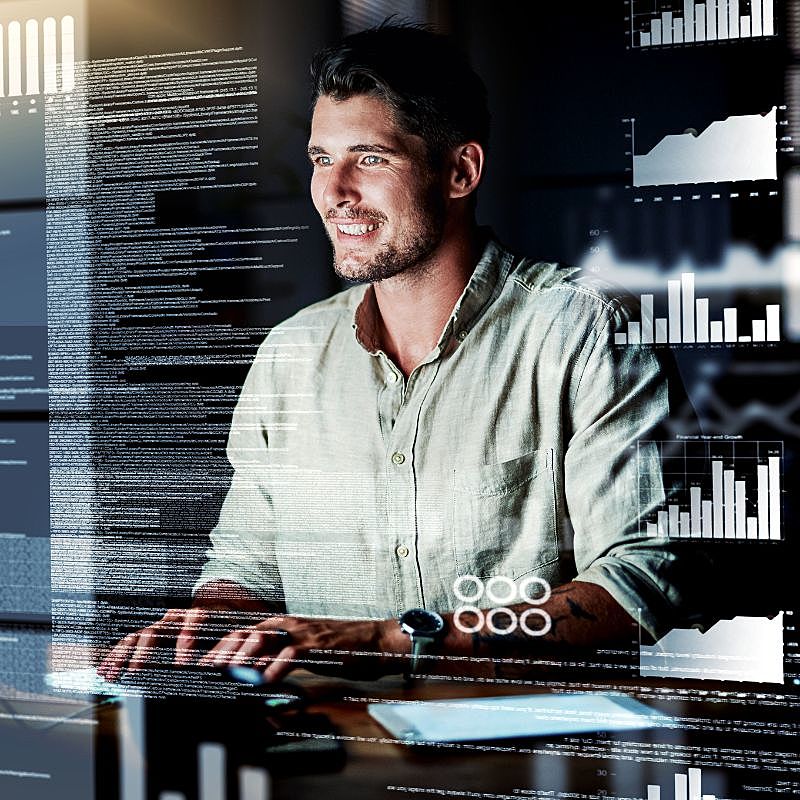
¿Qué es una Arquitectura de Datos Moderna y por qué es esencial para la Digitalización Industrial? Una arquitectura de datos moderna es una pieza fundamental en el proceso de digitalización industrial. Permite a las empresas gestionar grandes volúmenes de datos de manera eficiente, mejorar la toma de decisiones y optimizar sus procesos mediante la automatización […]