Las industrias manufactureras se están preparando enérgicamente para una transformación importante gracias al IIoT (Industrial Internet of Things), un nuevo modelo de producción que permite convertir los sistemas tradicionales en operaciones interconectadas y dinámicas.
En muchas áreas y segmentos de la economía, el IIoT está produciendo grandes cambios, sobre todo en giros como la logística, rastreo satelital, tracking de archivos y monitoreo sistemático de maquinaria. Por ello, se espera que la nueva generación de comunicación impulsada por la tecnología 5G dé el impulso maestro para posicionar un nuevo paradigma e incluya todas las industrias que faltan por sumarse.
Ahora bien, el propósito de este contenido es mostrar específicamente aquellos sistemas que pueden añadirse a esta nueva metodología y, con ello, transformarlas en operaciones interconectadas dentro de una industria.
Veamos los ejemplos más claros dentro de múltiples sectores de la economía.
Sistemas empresariales
Las operaciones interconectadas en este segmento, impulsadas gracias el IoT, conecta los dispositivos en los procesos de negocios para disminuir el riesgo tácito que existe al ejecutar tareas manuales.
Ahora bien, repasemos breve, pero cuidadosamente los sistemas empresariales que pueden ser parte de operaciones interconectadas con el IIoT.
1. ERP
Hay muchas formas de integrar un sistema ERP a una solución IIoT, por ejemplo, al automatizar procesos manuales como ejecutar órdenes de mantenimiento a través de un software de cloud computing.
Otro aspecto que evidencia la necesidad y las posibilidades en el campo del ERP son informes de salud de los dispositivos que se utilizan en el día a día, para obtener datos relevantes y oportunos a través del monitoreo y permitir un flujo de trabajo constante.
2. MES
Los sistemas de ejecución de fabricación o MES (Manufacturing Execution System) son usados relativamente en casi todas las industrias manufactureras modernas, sin embargo, la automatización basada en la nube y las plataformas SaaS están cambiando poco a poco este segmento de producción.
De hecho, un informe por parte de la consultora Gartner sugiere que para 2024 el 50% de las soluciones MES incluirán plataformas IIoT para brindar una gestión en tiempo real de las transacciones diarias.
Entendiendo que las plataformas de IoT Industrial sugieren una clase de solución más allá de un elemento individual, plataforma o tecnología podemos llegar a adivinar que es un recurso útil, por ejemplo, para conectar los procesos en la planta de producción con los sistemas activos que se ejecutan dentro de ella.
3. CRM
Teniendo en cuenta todo lo anterior, no es extraño pensar que una plataforma de Internet de las Cosas Industrial pueda generar sinergia con una solución como el CRM (Customer Relationship Management). Podríamos imaginar fácilmente los resultados provocados por esta unión, por ejemplo:
- Perfiles de clientes completos: para generar una vista ampliada y multidimensional de los datos, incluyendo información de redes sociales, dispositivos, entre otros.
- Inclusión predictiva: a través del análisis de las necesidades y comportamientos históricos para prever necesidades futuras.
- Estrategias de precios: nutriéndose de datos en tiempo real para generar nuevos y mejores lineamientos de precios dinámicos, motor de lógica y cálculo para resultados más precisos.
- Automatización: donde ya de por sí el CRM permite automatizar, sin embargo, maximizando la potencia entre la comunicación que existe entre el dispositivo o área de la empresa y el medio utilizado por el cliente para reaccionar rápida y eficientemente a sus requerimientos.
PLC’s
El controlador lógico programable o PLC que es uno de los pilares de la automatización industrial está a punto de experimentar varios y drásticos cambios en combinación al movimiento del IIoT.
La arquitectura original del PLC estuvo prediseñada para adaptarse a aplicaciones propias, sin embargo, con muchas limitaciones. En este sentido, el IIoT ha permitido flexibilizar la cooperación entre sistemas, permitiendo que cada PLC individual coexista y comparta información con otro, y no solo eso, también al estimular el trabajo conjunto con sistemas que funcionan tras el proceso de manufactura.
Todo esto ha generado nuevos beneficios para la industria, por ejemplo, la habilidad de que cada uno de los PLC’s en la red puedan reaccionar entre ellos ante eventos externos, como un cambio a último minuto de un cliente, para mejorar los tiempos de respuesta y maximizar la eficiencia operacional.
Robots
La posibilidad de monitorear la producción en una planta operada a través de la robótica y sincronizar numerosos dispositivos y piezas de hardware para que puedan trabajar al unísono en la consecución de un objetivo en común es otro de los tantos usos que tiene el IIoT en cuento a las operaciones interconectadas.
En el pasado, las compañías rara vez invertían en piezas de robótica sin asegurarse que esos elementos fuesen compatibles con los dispositivos ya incorporados en su ambiente de trabajo.
Sin embargo, con el avance en el IIoT, ahora mismo es posible encontrar robots industriales que pueden comunicarse con otros a través de la nube. Entonces, los colaboradores de la empresa pueden configurar varios robots para manejar necesidades particulares y visualizar las estadísticas de cada máquina en una plataforma especializada.
Maquinaria antigua
Ahora bien, para moverse eficientemente hacia la industria 4.0 es necesario adaptar la maquinaria antigua o legacy dentro de las plantas de producción para generar operaciones integradas realmente cooperativas. Esto es porque una gran porcentaje de las empresas manufacturaras dejan que sus sistemas, dispositivos o equipos antiguos realicen el trabajo de producción.
De hecho, un estudio elaborado por Broad Group señala que el 76% de los que toman decisiones en las industrias admiten que sus sistemas legacys no permiten una salida fluida de información, lo que evita que la automatización genere real impacto en la eficiencia.
Al llevar la maquinaria antigua hacia el IIoT, los manufactureros pueden empezar a entender mejor el desempeño de su planta de producción a través de datos especialmente relevantes. Conectar el equipo y los sistemas brindan una mejor visibilidad, monitoreo remoto de maquinaria y reportes precisos del desempeño.
¡Ya está!
En este punto ya conoces los elementos y áreas que pueden llevar a operaciones interconectadas mucho más eficientes y de provecho para las empresas. Es momento de dejar que la automatización impacte positivamente las actividades y que la transformación digital guíe a la organización a nuevos hitos de productividad.
Si deseas complementar tu lectura y seguir aprendiendo sobre esta tan interesante área, te invitamos a leer el siguiente contenido:
Conectividad industrial: ¿por qué es clave en estos tiempos?
Etiquetas:
Artículos relacionados
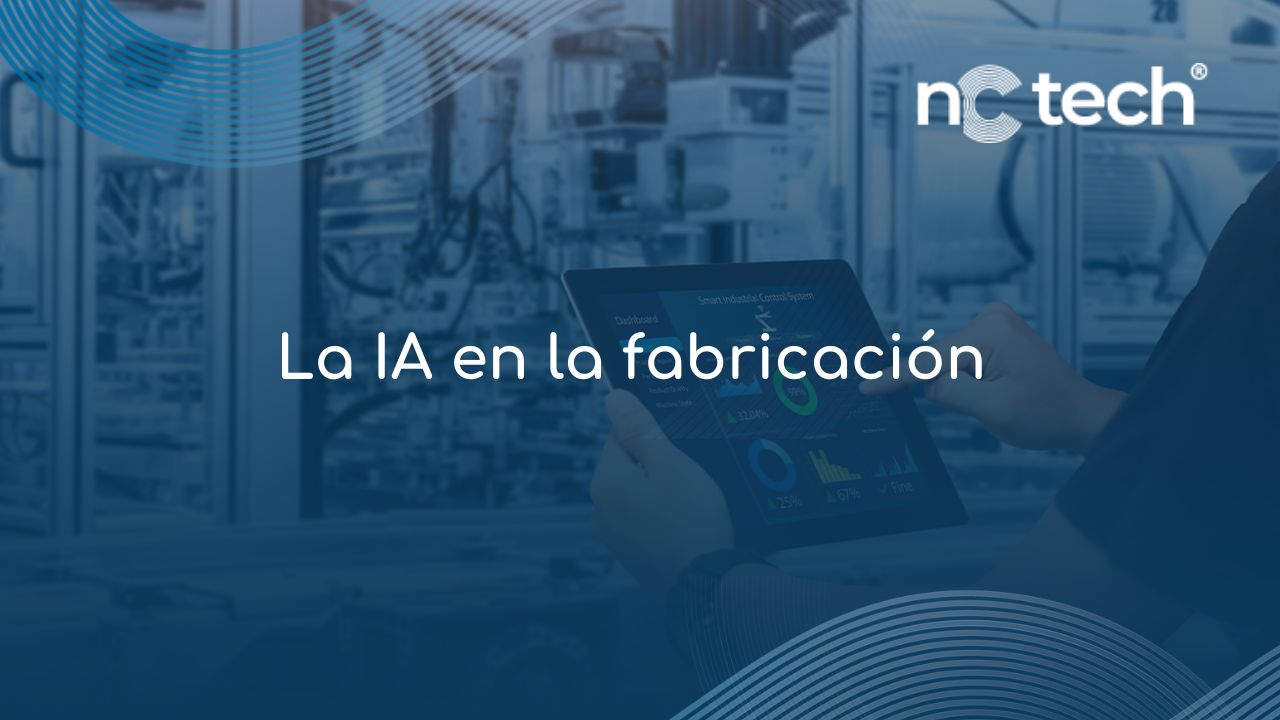
La inteligencia artificial (IA) ha emergido como un motor clave de transformación en la industria manufacturera, revolucionando la forma en que las fábricas operan y cómo los productos son fabricados. Con la capacidad de realizar tareas complejas, optimizar procesos, y predecir fallos, la IA está no solo cambiando el panorama de la fabricación, sino también abriendo nuevas […]
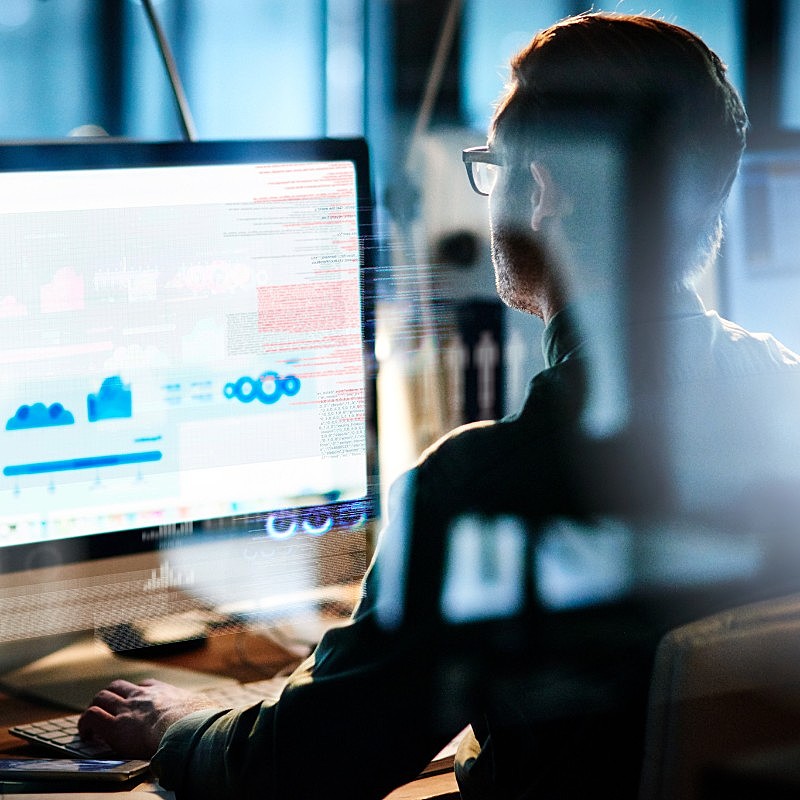
La Evolución de la Ingeniería de Proyectos La ingeniería de proyectos bien gestionada permite optimizar recursos, tiempo y alcance, incrementando la productividad en empresas de cualquier tamaño. Aunque no es una carrera en sí misma, emplea estrategias y técnicas de digitalización de procesos, clave en la Industria 4.0, para rentabilizar operaciones. ¿Qué es la ingeniería […]
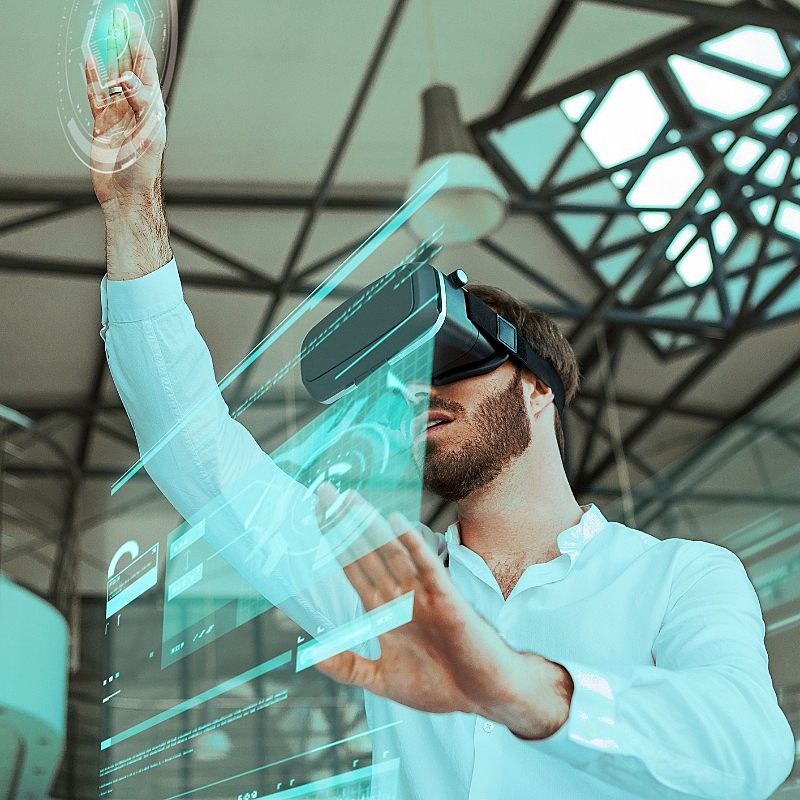
Cómo mejorar la retención de clientes en la manufactura: 4 estrategias clave En la industria manufacturera, muchas empresas se enfocan en la adquisición de nuevos clientes, pero es esencial no descuidar la retención de clientes. Retener a un cliente existente es más rentable que adquirir nuevos, y también es más eficiente en términos de costo […]